Product Lines Smart Plastics & New Mobility Truck, Bus & Agricultural Applications Painted Exterior & Acoustic Solutions Powertrain & Battery Solutions Underbody Solutions
Working at POLYTEC Job portal Apprentices / Trainees School pupils / Students Experienced professionals Learning & Development POLYTEC Leadership Principles Benefits FAQ & application tips Career and job fairs
Overview Equity Story News Share Calendar Publications Telephone conference & presentation Annual report 2023 Annual General Meeting Corporate Governance Contact IR Information Service
Overview Strategy & Mission statement Management History Downloads & Media Upcoming Events Locations Organisation chart Code of Conduct & Human Rights Whistleblowingportal Blog
Overview Ambition paper Strategy Field People Strategy Field Energy Strategy Field Production Strategy Field Legislation Strategy Field Customers Strategy Field Products Strategy Field Financial market Strategy Field Supply Chain Sustainability in the Annual Report 2023
![[Translate to Englisch:] [Translate to Englisch:]](/fileadmin/_processed_/e/e/csm_Header_670e97173d.jpeg)
INNOVATIVE, EFFICIENT, DYNAMIC
Learn everything about both the innovative solutions created by the POLYTEC SOLUTION FORCE and our product lines.
FIND OUT MORE
![[Translate to Englisch:] [Translate to Englisch:]](/fileadmin/_processed_/e/e/csm_Header_670e97173d.jpeg)
INNOVATIVE, EFFICIENT, DYNAMIC
Learn everything about both the innovative solutions created by the POLYTEC SOLUTION FORCE and our product lines.
FIND OUT MORE
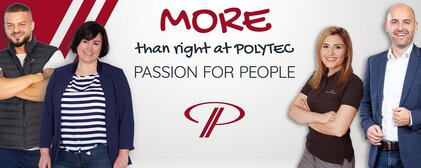
More than right at POLYTEC
Become a part of our team.
To the job portal
![[Translate to Englisch:] [Translate to Englisch:]](/fileadmin/_processed_/d/0/csm_GB23Theme_94edf1f62a.png)
DIGITAL ANNUAL REPORT 2023
Discover the latest digital annual report of the POLYTEC GROUP!
DISCOVER NOW
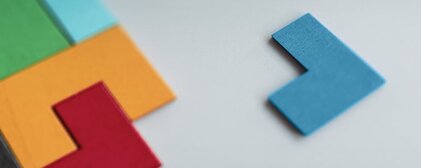
Strategy & Mission statement
Find out more about the strategy of the POLYTEC GROUP.
Find out more
![[Translate to Englisch:] [Translate to Englisch:]](/fileadmin/_processed_/f/3/csm_Nachhaltigkeit_Menue_629d33ed20.jpg)
GoNeutral 2035
Find out more about GoNeutral 2035